Understanding the Cylindrical Cell Manufacturing Line: A Comprehensive Guide
The production of cylindrical lithium-ion cells, such as the widely used 18650, 21700, or 4680 cells, is a complex and highly automated process that requires precision, consistency, and efficiency. A Cylindrical Cell Manufacturing Line integrates multiple stages of production into a seamless workflow, ensuring high-quality cells are manufactured at scale. In this blog post, we’ll explore what a Cylindrical Cell Manufacturing Line is, its key components, how it works, and why it's critical for modern battery production.
---
●What is a Cylindrical Cell Manufacturing Line?
A Cylindrical Cell Manufacturing Line is an advanced industrial setup designed to mass-produce cylindrical lithium-ion batteries. It combines specialized machinery, automation systems, and quality control processes to ensure consistent cell performance, safety, and reliability. These lines are capable of producing millions of cells annually, catering to applications ranging from consumer electronics to electric vehicles (EVs) and energy storage systems.
The manufacturing line typically consists of several interconnected stations, each responsible for a specific stage in the production process.
---
●Key Stages in Cylindrical Cell Manufacturing
1. Material Preparation
- Coating: Active materials (e.g., lithium cobalt oxide for cathodes, graphite for anodes) are mixed with binders and conductive additives to form slurries. These slurries are then coated onto metal foils (aluminum for cathodes, copper for anodes).
- Drying: The coated foils are dried to remove solvents, leaving behind a uniform layer of active material.
- Rolling: The dried foils are compacted using rollers to achieve the desired thickness and density.
2. Electrode Cutting and Slitting
- The coated foils are cut into precise dimensions to match the specifications of the cylindrical cell design. This ensures proper alignment during winding.
3. Winding
- The cathode, anode, and separator layers are wound together into a tight spiral "jelly-roll" configuration. Precision winding is critical to prevent misalignment, which could lead to internal short circuits or uneven current distribution.
4. Insertion into Casing
- The wound electrode assembly is carefully inserted into a cylindrical metal casing. The casing serves as both a structural component and one of the electrical terminals.
5. Electrolyte Filling
- The casing is filled with electrolyte, a liquid or gel that facilitates ion movement between the cathode and anode during charge/discharge cycles. Proper filling ensures optimal electrochemical performance.
6. Sealing
- The top cap is sealed onto the casing, creating a hermetic seal to prevent leaks or contamination. Electrical connections are established through the cap.
7. Formation
- The assembled cells undergo formation cycles, where they are charged and discharged under controlled conditions to activate the battery chemistry. This step is crucial for evaluating initial cell performance metrics, such as capacity, voltage stability, and internal resistance.
8. Testing and Quality Control
- Cells are subjected to rigorous testing procedures, including:
- Capacity testing
- Voltage and resistance measurements
- Thermal cycling
- Safety tests (e.g., overcharge, short circuit, impact)
- Defective cells are identified and removed from the production line.
9. Packaging
- Qualified cells are labeled, sorted, and packaged for shipment to customers or further integration into battery packs.
---
Li Ion Battery Cylindrical Cell Production Line
●Why is a Cylindrical Cell Manufacturing Line Important?
Cylindrical lithium-ion cells are among the most widely used battery formats due to their high energy density, reliability, and scalability. The manufacturing line is critical for several reasons:
1. High Throughput: Automated production lines enable the mass production of cells, meeting the growing demand for batteries in EVs, consumer electronics, and renewable energy storage systems.
2. Consistency: By minimizing human intervention, the manufacturing line ensures uniformity in cell performance and quality.
3. Cost Efficiency: Large-scale production reduces per-unit costs, making batteries more affordable for widespread adoption.
4. Customization: Modern manufacturing lines can be configured to produce various cell sizes and chemistries, catering to diverse application needs.
5. Safety Assurance: Advanced quality control systems integrated into the line help identify and eliminate defective cells, ensuring safe and reliable products.
---
●Types of Cylindrical Cells Produced
Cylindrical Cell Manufacturing Lines can produce a variety of cell sizes and configurations, including:
1. 18650 Cells: Widely used in laptops, power tools, and early EV models.
2. 21700 Cells: Larger and more energy-dense than 18650 cells, commonly used in modern EVs and high-power devices.
3. 4680 Cells: A newer format developed by Tesla, offering significantly higher energy density and faster charging capabilities.
4. Custom Sizes: Some manufacturers produce non-standard cell sizes tailored to specific customer requirements.
---
●Advancements in Technology
Modern Cylindrical Cell Manufacturing Lines incorporate cutting-edge features to enhance productivity, precision, and flexibility:
- High-Speed Automation: Robots and conveyor systems streamline operations, reducing cycle times and increasing throughput.
- Real-Time Monitoring: Sensors and data analytics provide instant feedback on key parameters, enabling proactive adjustments and better quality control.
- Modular Design: Flexible layouts allow manufacturers to easily reconfigure the line for different cell types or production scales.
- Integration with IoT: Cloud-based platforms enable remote monitoring, predictive maintenance, and collaborative research and development.
---
●Challenges in Cylindrical Cell Manufacturing
Despite their advantages, Cylindrical Cell Manufacturing Lines face several challenges:
1. Technical Complexity: The production process involves numerous variables, requiring skilled personnel and sophisticated equipment to maintain consistency.
2. Initial Investment: Setting up a fully automated manufacturing line can be expensive, though economies of scale often offset these costs over time.
3. Scalability Issues: Rapid advancements in battery technology may render existing lines obsolete unless they are designed for adaptability.
4. Environmental Concerns: Managing waste materials, such as scrap electrodes and electrolytes, is essential to minimize environmental impact.
---
●Future Trends in Cylindrical Cell Manufacturing
As battery technology continues to evolve, several trends are shaping the future of Cylindrical Cell Manufacturing Lines:
1. Solid-State Batteries: Transitioning from liquid electrolytes to solid-state electrolytes will require significant changes in manufacturing processes and equipment.
2. AI and Machine Learning: These technologies will play an increasingly important role in optimizing production workflows, predicting equipment failures, and improving product quality.
3. Sustainability Initiatives: Manufacturers are focusing on reducing carbon footprints and recycling materials to promote environmentally friendly practices.
4. Increased Energy Density: Advances in materials science and engineering will enable the production of cells with higher energy densities and faster charging capabilities.
---
●Conclusion
The Cylindrical Cell Manufacturing Line is the backbone of modern battery production, driving innovation and supporting the global transition to sustainable energy solutions. By integrating advanced automation, real-time monitoring, and flexible design, these lines ensure high-quality, cost-effective cells that meet the demands of diverse industries.
Whether you're designing batteries for electric vehicles, consumer electronics, or large-scale energy storage systems, understanding the capabilities and significance of Cylindrical Cell Manufacturing Lines is essential. With continued advancements in technology, we can look forward to even more efficient, reliable, and sustainable battery production in the years to come.
---
Feel free to share your thoughts or experiences with Cylindrical Cell Manufacturing Lines in the comments below! If you have questions about specific aspects of the production process or equipment, don't hesitate to ask.
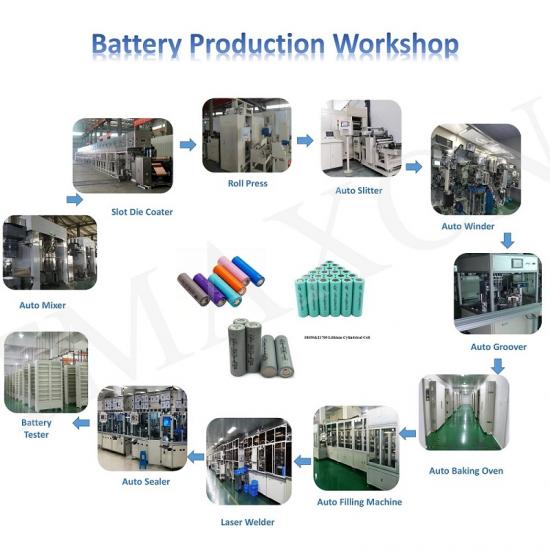